CAROUSELS
Carousels are AS/RS systems being used
for main storage, kitting,
progressive assembly, work-in-process (WIP) in many industries
that involve dynamic small-parts storage. A carousel can be defined
as "a series of bins that are linked together in a continuos
chain and mounted on an elongated oval track" (Weiss,
Cramer, 1988). The track is generally horizontal, but in some
situations it is vertical to save floor space.
A new approach is the " twin-bin carousel",
which provides two faces for pickup in each carrier.
When activated, the entire carousel revolves, bringing
the desired carrier (bin) to the
picker (in
a horizontal carousel, the speed is in the vicinity of 80 feet/min).
When the carousel stops, the operator can then pick the product
from the appropriate shelf.
Sometimes a fixed ladder or platform
is used in order to provide better reach. All the systems that
are presented here use single-tier shelving, meaning that
there is only one vertical level of pickers. In some cases better
productivity is achieved by use of double- and
triple-tiered
systems. This means that there are two or three floors from
which the pickers can retrieve products from the carousel(s).
The basic idea behind the development of carousels is that
the product to be picked is brought automatically before the picker,
rather than requiring him to walk through aisles searching. This
saves time, particularly in the high-volume order-picking applications.
Carousels are modular in design. By connecting standard drive,
idler and intermediate sections a final configuration is generated.
This modular design enables shorter lead times, quick installation,
and ease of extension or movement (Weiss, Cramer, 1988).
Implementation of carousel systems can bring broad benefits.
As an example, Canadian publisher McGraw-Hill obtained many benefits,
some of which are listed below, when they switched to a smaller
facility, coupled with choosing the right material handling equipment
(Gould, 1993):
- Order-picking productivity increased 200%, going from 32 to
100 lines per hour.
- Average order-filling time decreased from 3 days to 1 day.
- An order backlog was eliminated.
- Warehouse space required decreased by 20%.
- A $1 million savings in building/operating costs has been realized.
Carousels can be fitted with automatic extractor mechanisms to
increase productivity. Automatic identification equipment, label
printers, manipulators, hoists, take-away conveyors, floor trucks
or lift tables, mezzanines, workers can be precisely positioned
at the pick-face to aid the flow of material (Trunk, 1994), (Forger, 1993).
An important point is that the interface equipment/personnel
to the carousel must not become bottlenecks that slow down the
carousel. The interfaces must be designed to keep the carousel
busy at all times.
Carousels are designed in varying sizes and capacities. In the
operations research literature, procedures and computer programs
have been developed to determine the system configurations given
considerations, constraints and goals. For a step-by-step procedure
for configuring a system (with examples) the reader is referred
to (Sharp, Eckert, Gibson, Houmas, Mardix, 1990).
(Bulla, 1986)
developed a software tool to determine the initial feasibility
of carousels as compared to other equipment.
There are certain considerations when deciding on which handling
equipment(s) in particular to use. Kardex Systems Inc. offers
the following checklist to help custom design a carousel for a
given facility (Trunk, 1994):
- What type of material will be stored, including size/weight
(item characteristics)
- What kind of activity can be expected for these items? (i.e.
what are the frequencies of retrieval, etc.)
- Will the carousel support production or a tool room, general
stores, etc.?
- What floor space and overhead area are available to the carousel
in length, width and height? (space constraints)
- What are the primary goals? Is it productivity improvement or
space savings? (objective function)
Benefits of Carousels
When itemizing the benefits of carousel systems, the approach
followed by (Weiss, Cramer, 1988) will be followed, and the major
benefits of carousels and benefits of computer-controlled carousels
will be presented seperately.
Major Benefits of Carousels:
- Labor Savings: Since the picker moves very little or
none at all from his current position, no time is wasted for walking
or searching for parts. It would not be misleading to state that
in typical static small-parts storage systems the bulk of the
retrieval time is wasted for these tasks. Another benefit is
that the picker can perform tasks such as processing paperwork,
weighing, counting parts while the carousel is busy retrieving
the part in front of him. The ideal case is when the
time that the picker spends for these tasks is equal to the time
that it takes for the carousel to retrieve the next item. In
this ideal case the picker and carousel utilizations are maximized.
- Ergonomic Benefits: By relieving the employees
from the task of walking up and down the aisles (which would be
the case in static storage schemes) employee fatigue is reduced
significantly. Especially in the case of carousels with vertical
movement capabilities, the load is brought to an easy-reach position
for the picker, providing ergonomic benefits.
- Increased Throughput: The picker can handle many carousels,
especially if the pick time is negligible compared to carousel's
travel time. This means that several parts will be coming to
the operator simultaneously, resulting in increased throughput.
(An analogy to this is the parallel computing concept in computer
science.) Throughput is even more increased in applications where
the shelf to be picked from is revolved automatically to the "golden
zone" of the picker.
There are research papers/articles available in literature on
mathematical models to increase throughput. Even
though solutions to individual cases in application would be customized,
some interesting insights are provided in these papers. An example
to these is that implementing double-carousel system is better
than implementing a single-carousel system with the same number
of carriers in total.
- Space Savings: Many carousels can be installed with
very little aisle space in between. A space narrow enough to
enable a repairman would be sufficient. This brings some savings
compared to conventional shelving.
- Increased Cube Utilization: A fixed ladder or platform
can result in better use of single-tier shelving. Special structures
for shelves and bins, and double- and triple-tiered systems help
boost cube utilization where constraints implied by product characteristics
and space permit.
- Improved Control of Employees: Since employees are observable
at all times, wandering will be eliminated. Pilfrage will drop
automatically where it occurs.
Major Benefits of Computer-Controlled Carousels:
- Possibility of Random Storage: With computer-controlled
part locations random storage of parts is possible. Since random
storage requires less space than dedicated storage, this will
increase the storage density. The benefits are even more if one
can increase flexibility through adjustable shelves.
- Sequenced Picking: Since the computer indexes the carousel
by bin location, an automatic sequencing can be done before the
carousel is automatically moved to the next best pick location.
This can reduce the retrieval time up to %100 (compared to the
simplest rule of moving the carousel in a single direction continuously)
under certain conditions (especially for high order rates and
low item densities). Again the reader is referred to the results
of academic research.
- Faster Replenishment: The feasibility of random storage
decreases replenishment costs, since the next replenishment is
simply going to be done at the next available space in front of
the replenishment worker/robot.
- Accuracy: Accuracy is a natural outcome of computer-controlled
operations.
- Simplified Inventory: Tracking inventory is possible
simply by requesting an inquiry to the database system. Typically
end-of-the-day inventory is printed from the computer at the end
of the day. Availability of consistent and dependable data for
inventory enables further analysis of inventory decisions and
applicability of operations research methods further in improving
inventory practices and layout.
- Integration: With use of computers, carousel systems
can be integrated into factory systems. An overall integrated
system provides possibilities for global optimization of the facility
operations, rather than losing time to explore local optima.
Additional Benefits of Vertical Carousels:
Besides the advantages described above, some additional benefits
of vertical carousels are listed for reference (Trunk, 1994):
- Space Savings: In most warehouses overhead space is underutilized.
Using vertical carousels, more space savings can be achieved
than horizontal carousels (when the ceiling poses no height restrictions),
because of the relatively small footprint.
- Better Ergonomics: Since parts are delivered to a selected
height, namely the "golden zone", for the convenience
of the order picker, ergonomic advantages are gained.
- Increased Safety: Small, costly items can be stored,
weighed, protected and accounted for more easily.
- Hazardous Materials Storage: Hazardous or flammable
material can be stored in vertical carousels with more safety,
since special vertical carousels can offer CO2
or Halon fire protection.
Disadvantages of Carousels
Some of the disadvantages of carousels are as follows:
- Cost: Carousel systems are more expensive than regular
shelves or racks.
- Replenishments: When there is a high turnover rate for
a product there will be a need for many replenishments, since
the bins have very limited space.
Design Considerations
Here are some suggestions in implementing carousels:
- Place the carousel where it will optimize product flow
- Interface equipment should
- not create bottlenecks and slow down carousel
- have enough buffer to keep the carousel busy at all times
- Use testing tools (such as simulation) to predict performance
There has been academic research on carousels with some important
results.
(Sharp et. al, 1990) have performed simulations to compare the performances
of different number of parallel carousels, and have obtained the
following chart:
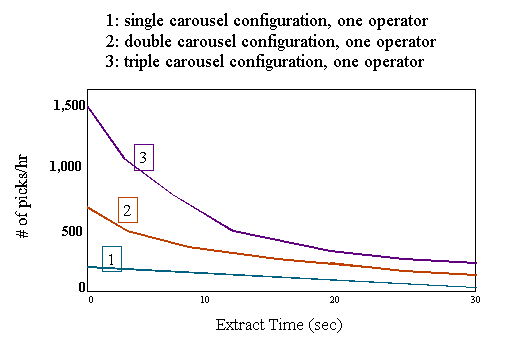
Another study (Koenigsberg) has shown that "S carousels of
N/S bins each is better than a single carousel of N bins"
[Figure]
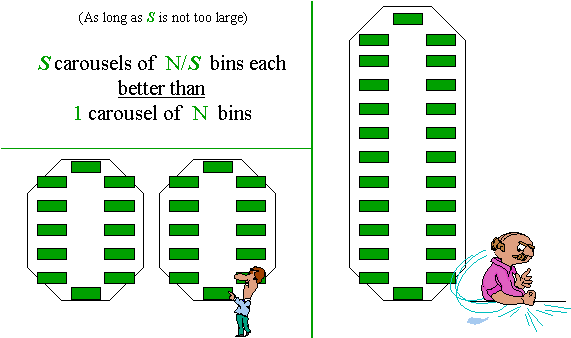